
SIDEMEKI
SIDEMEKI intended use

Why is X-ray inspection the new standard in the food industry?
X-ray inspection of primary packaging has made Critical Control Points an important part of the overall traceability in the supply chain, which starts with the raw material and ends with the purchase of the products by the consumer.
It is well known that X-ray systems are able to detect non-metallic contaminants. However, when inspection is performed on individually packaged products, X-ray inspection can add tremendous value in terms of overall quality control (e.g. headspace and seal inspection) and traceability. This reduces the number of complaints and provides consumers with safe and high quality products.
And when new local or global quality and safety certifications (e.g. HACCP, HARCP, FSMA or BRC) become necessary, inline X-ray inspection systems meet and exceed the requirements of all regulations. The introduction of X-ray inspection offers you the opportunity to open up new markets, comply with all standards and change packaging materials without restrictions.
SIDEMEKI
SIDEMEKI intended use

Why is X-ray inspection the new standard in the food industry?
X-ray inspection of primary packaging has made Critical Control Points an important part of the overall traceability in the supply chain, which starts with the raw material and ends with the purchase of the products by the consumer.
It is well known that X-ray systems are able to detect non-metallic contaminants. However, when inspection is performed on individually packaged products, X-ray inspection can add tremendous value in terms of overall quality control (e.g. headspace and seal inspection) and traceability. This reduces the number of complaints and provides consumers with safe and high quality products.
And when new local or global quality and safety certifications (e.g. HACCP, HARCP, FSMA or BRC) become necessary, inline X-ray inspection systems meet and exceed the requirements of all regulations. The introduction of X-ray inspection offers you the opportunity to open up new markets, comply with all standards and change packaging materials without restrictions.
What makes tall food products special for X-ray inspection?
With SIDEMEKI, this split focus challenge is solved with the option for two individual X-ray generators to provide the sharpest image for the entire high food product. In this way, the system continues the globally recognized Mekitec technology and ethos of delivering the best value and performance.
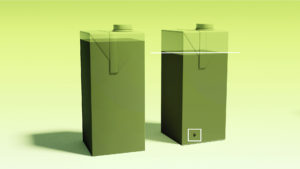
What should be taken into account in production lines with high food content?
Ensuring a smooth production flow and the rejection of non-conforming products is crucial for these types of packaging and places higher demands on the design of the inspection system. For this reason, SIDEMEKI was designed without lead curtains and is equipped with comprehensive product guides to ensure that food packaging moves effortlessly through the system and inspection.